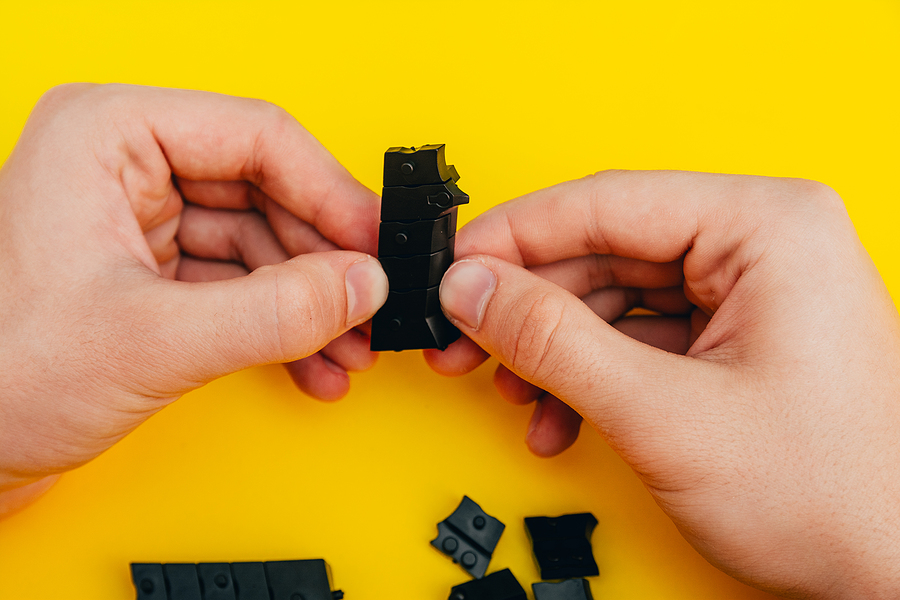
The act of prototyping is typically performed to test various part designs to create the best product, and sometimes it’s required to show multiple design elements to prospective investors. Regardless, prototype development is integral to the plastic injection molding process, as the final product should mirror the designer’s image. However, there are often time constraints on part manufacturing, so individually prototyping different molds can be wasteful. That’s where rapid part prototyping comes in to play.
What is Rapid Part Prototyping?
Rapid part prototyping is a way of quickly testing a finished plastic part before beginning mass production. A computer model is usually first created by engineers in computer-aided design (CAD) software – our preferred software is SolidWorks CAD. It then involves the formation of a scale model of a plastic part through a number of processes – 3D printing, injection molding, and CNC machining being the most common. This method is so valuable in that it allows for rapid testing of prototypes and quick modification without the worry of costly mistakes arising during full manufacturing.
Why You Should Involve Manufacturers During the Design Process
While creating a digital model inhouse can take care of the design aspect early, working early with manufacturers allows you to take advantage of design choices based on manufacturing practicalities. A manufacturer is more likely to understand the plastic’s properties, the injection molding machine’s limitations, and how to produce more cost-efficient parts. If you don’t communicate your needs to your manufacturer, it can defeat the purpose of rapid part prototyping due to the risk of producing a low-quality part. Additionally, manufacturers will also know the prototype process suitable to your needs.
What is the Difference Between Rapid Part Prototyping Methods?
Your options depend on your needs. There’s a complex web of processes and branching methods for rapid part prototyping, but we’ll focus on the three most common.
Injection Molding
This method is ideal for businesses looking to quickly transition into high-volume production. This method is often used to create high-quality prototypes with composite features. While injection molding has a high upfront cost and a longer processing period, it’s a much faster transition from the prototype stage to full production, as you’re prototyping both the mold and the part at the same time. It’s also recommended for businesses needing a high number of prototypes.
3D Printing
3D printing is an affordable and versatile option when it comes to prototyping. 3D printing machines can heat thermoplastics and layer the material into the ideal part. This process offers speed and detail and saves you from building a costly mold, but the finished product will have visible layer lines that will need to be filed down and sometimes painted. It’s not an ideal process for businesses seeking high-volume production.
CNC Machining
CNC machines use computer-controlled cuts to remove material from a solid block of plastic. It pulls information from a CAD file and quickly breaks down the data into milling commands. This process is fast and can produce larger prototypes. It also allows for a wider surface finish than other methods of rapid prototyping. However, although a mold isn’t required, it’s generally costlier to create parts and is a slower mass production process than injection molding.
Which rapid part prototyping method best fits your needs depends on the constraints of your project. It’s important you speak to your manufacturer if you require a prototype to showcase to investors or need to expedite the manufacturing process. In particular, if you are interested in injection molding rapid part prototyping, we here at Midstate Mold can help you. Our experience grants us the ability to help you with your prototype design and carry your vision through to the mold making and production process. Contact us today to determine if injection molding is the right method for your project.