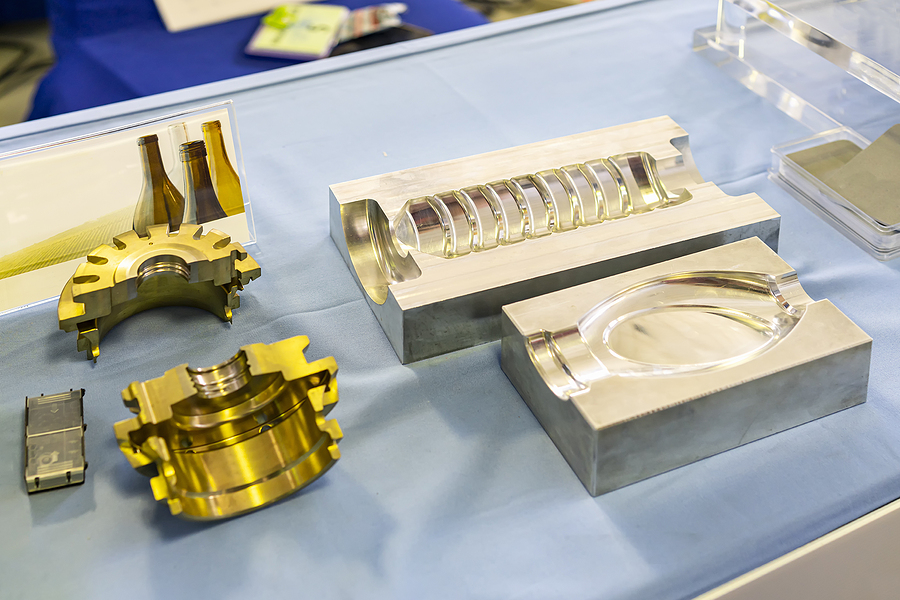
Many believe prototyping is just an extra, unnecessary step in the injection molding process, which is a misconception that can result in severe production line disruptions and forfeiture of time and money. In fact, some believe it increases costs and inhibits development and production times, but in reality, it does the opposite. Proceeding with a custom injection molding without prototyping often results in a series of tool adjustments that can become both time-consuming and expensive. Let’s review precisely how prototype tooling in injection molding accelerates production and saves you time and money.
What is Injection Molding Prototype Tooling?
Prototype tooling is essentially a learning tool for manufacturers: they’re designed for engineers to learn the viability and reliability of a mold without expensive alterations. The prototype tool is typically not as robust as the final product, and it may be made of aluminum or mild steel to save money on both cost and labor. Their main purpose is to prove that the part design will work before investing in a more expensive production mold. It’s a surefire way to steer clear of part defects, prevent production line mishaps, produce stronger and cheaper parts, and lengthen the life of molds.
Elements of Prototype Tooling that Accelerate Injection Molding Production
Customers are often dismayed to find that prototype tooling accounts for roughly 20% to 40% of the overall production costs, depending on the complexity. While this seems a significant investment, it allows injection molding manufacturers to visualize the application’s capabilities and helps them to streamline the production, saving you money in the long run. The advantages to prototype tooling include:
- Testing Plastics: During the prototyping stage, the performance of the plastics being considered can be easily tested and assessed before production to avoid making an uninformed, major financial decision.
- Confirming Part Geometry: Prototyping is perfect for rooting out any potential defects in the part design. If defects are uncovered, a prototype can be easily manipulated with cuts and welds. Likewise, new dimensions can be tested to accommodate for wall thickness or ribbing.
- Perfecting Gate Locations: Using a prototype tool allows the manufacturer to properly apply gates to the mold and apply cuts and welds to adjust gate locations. Doing so on a production tool limits its lifespan and performance and adds cost and time to production.
- Assessing Complex Geometry: If the part requires the use of sliders or other forms of undercuts, these features can be tested during the prototype phase. Also, hand-loaded inserts can be used in place of actual sliders, bump-offs, or other complex design features.
All these elements combined lead to hastened production, as it’s quicker and cheaper to make adjustments to a prototype tool compared to a tool being used in production. Prototype tooling leads to a final design that requires fewer revisions, an optimized cycle time, and reduced overall costs on the backend.
Pairing Prototype Tooling with Rapid Part Prototyping for Further Acceleration
While making sure the mold is suited to the challenge, it’s also important to ensure the part meets your requirements before mass production. Rapid part prototyping uses computer-aided design (CAD) software – our preference is SolidWorks CAD – to create a scale model of a plastic part. Like prototype tooling, this process allows you to test the product and make quick and easy modifications before production. Both prototype tooling and rapid part prototyping require close work with the manufacturer during the design process and will help avoid costly defects or oversights during production.
When speed and cost-efficiency are required, it makes sense why prototype tooling in injection molding accelerates production. Troubleshooting both your tooling and parts during the development phase goes a long way in limiting time-consuming mistakes during production. At Midstate Mold, we have decades of experience guiding our clients through the prototype process and executing their low- or high-volume production from beginning to end. If you require a manufacturer dedicated to the details, contact us today.