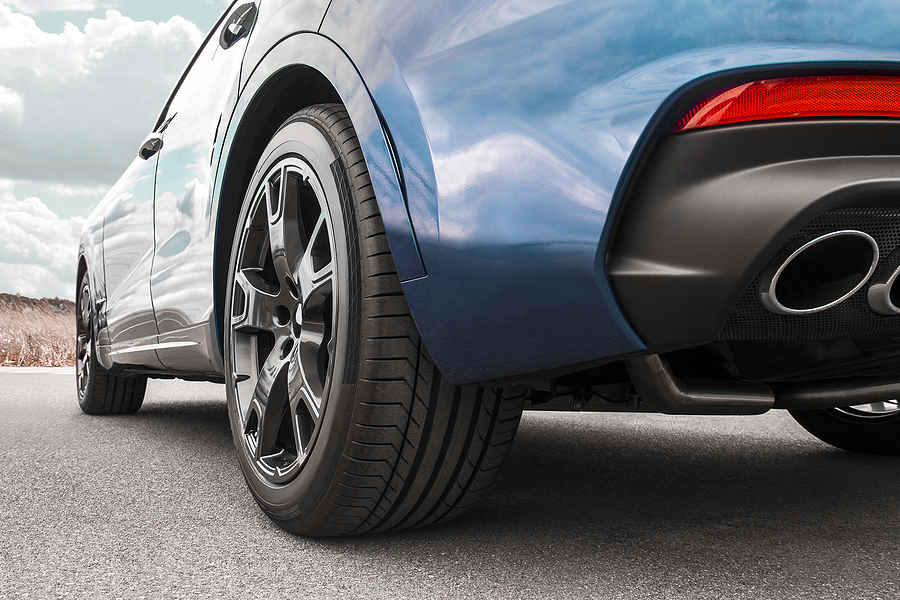
We’ve come a long way since the Model T, transitioning away from heavy metal beams and brackets to lightweight yet durable plastics. Today, plastic parts support a wide variety of car functions, from the pedal and seat components to the powertrain and fuel system. There are several benefits to using plastics in car manufacturing, and skilled injection molders are well-versed in matching the right polymers to a car part’s performance needs. To discover just how useful this material can be, let’s review the benefits of plastic parts in the automotive industry.
Why Use Plastic Parts in the Automotive Industry?
Of the 30,000 parts used in today’s vehicles, nearly one-third are made of plastic, according to Nexant, and there’s a reason for this popularity. Plastic is cost-efficient and weighs significantly less than conventional metals. With fuel efficiency not only being a big selling point but also a growing focus of industry regulations, reducing vehicles’ weights is vital. Furthermore, plastic is frequently more durable than metal and is resistant to corrosion and rust. Car parts are subject to a lot of abuse – both via road hazards and weather – and plastics are best suited to meet these challenges.
What Are Some of the Common Plastics Used in the Automotive Industry?
The automotive industry relies on high-performance plastics to provide safety and security for drivers. Some of the common thermoplastics used in automotive design include:
- Polypropylene: This is the most frequently used plastic in vehicles. Polypropylene boasts impressive chemical, heat, and impact resistance, and you’ll often find it being used for car bumpers, electrical housings, and scuff plates.
- Polyvinyl Chloride: Commonly known as PVC, this plastic flame retardant and can be used for either flexible or rigid components. This plastic is used for most vehicle dashboards and the body of the car.
- Polycarbonate: Polycarbonate is an impact-resistant thermoplastic also often used for car bumpers and headlight lenses. It’s also weather-resistant and very lightweight, contributing to the vehicle’s fuel efficiency.
- Acrylonitrile Butadiene Styrene: Also known as ABS, this material is very durable and can be used for various car components, from the dashboard and steering wheel cover to automotive body parts. This plastic is capable of absorbing and redistributing energy from impacts.
While these are some of the most used plastics in the automotive industry, their benefits extend far beyond those listed here.
Additional Injection Molding Processes Used in the Automotive Industry
There’s a wide range of processes the industry takes advantage of to ensure customer satisfaction. Just a few of the secondary benefits of using plastics in vehicle manufacturing include:
- Color: Colorant additives can be applied to plastic resins to achieve the color of the manufacturer’s or driver’s choice.
- Inserts: Thermoplastics can work cohesively with metal connectors, which is ideal for components that require non-plastic inserts.
- Laser Etching: A laser can be used to etch a design or the manufacturer’s logo onto plastic parts, such as the dashboard.
There are several other benefits, such as imaging application techniques – including silk screening and pad printing – and a variety of other custom processes.
Discovering the many applications of plastic parts in the automotive industry can help you understand just how versatile thermoplastics can be. With the help of plastic injection molders, vehicle manufacturers and many other industries have been able to find better alternatives to short-lived and more expensive materials like metal. At Midstate Mold, we can help you design and create durable plastics parts for your next project, and we can accomplish every step of the injection molding process, from prototype development to production. If you require high-quality plastic parts, contact us today.