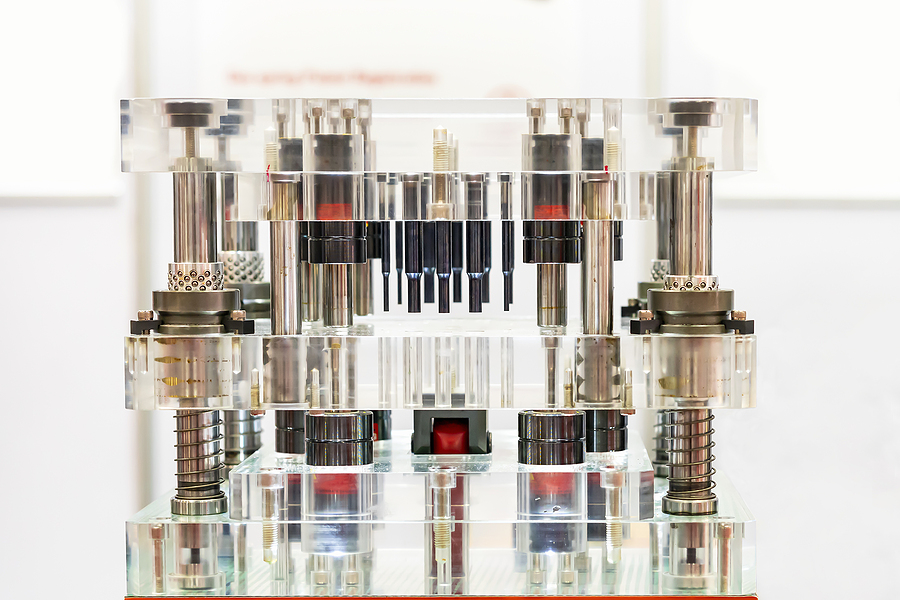
When plastic parts become stuck in a mold, it can result in part defects, breakage of mold components, manufacturing delays, and increased costs. That is why carefully designing an efficient ejection system is key to achieving optimal output and final quality products. To design a system that ejects parts easily, quickly, and consistently, the engineer should pay considerable attention to the ejection surface area, the location, and the ejection type. Let’s take a closer look at these three considerations when designing a plastic molding ejection system.
1. Applying a Sufficient Ejection Surface Area
A plastic part’s size and geometry play a large role in determining the ejection surface area. If the area is insufficient, it can result in part deformities, breakage, and longer cycle times. The best practice is to lean towards using larger ejection surface areas when prototyping. If your part has smaller ejection features, it will require smaller ejection components, which can introduce a higher risk of breakage due to their fragility. Furthermore, the knockout clearance holes should not measure under 3/64 of an inch in diameter. If the part’s walls are thin, custom-made ejector sleeves will be required.
2. Planning Out Ejector Locations
You ideally want the ejection surface to be flat, as it will allow the knockout pins to stabilize at a uniform height. In cases where your part is unable to conform to a flat shape, the ejector components can be customized to adhere to the part’s geometry. Severe contours in your part may require alterations to its design, as the slope will not provide a surface that is parallel enough to the parting line, making it more difficult to knock out. You also want your ejection points to be located as the deepest areas of your part and to err on the side of caution: a molder may apply more ejectors than required.
3. Determining the Ejector System Type
Just as plastic molded parts come in many shapes and sizes, so too do ejector systems. These various systems leave different marks on the plastic, and each requires its own level of maintenance. Some of the common ejector system types include:
- Ejector Pins: These are the simplest and most cost-effective of the ejection systems. Ejector pins leave circular ejection marks on the plastic part.
- Blade Ejectors: If ejector pins can’t fit within the ejection area, blade ejectors are a great alternative. They have flat, rectangular pins that can eject the part from thin regions.
- Ejection Sleeves: These distribute pressure evenly across circular features. The residual mark matches that of the sleeve shape.
- Ejector Bars: This is typically a more costly method, but it’s a great option for ejecting a part along lengths of flat surfaces. They tend to be larger than pins and require some customization.
- Stripper Systems: This is used to eject a part along its perimeter. A molder is required to ensure the stripper plate sits flush with the injection mold – otherwise, flashing can occur.
Each system comes with its own cost and level of maintenance, but if your team with an experienced plastic injection manufacturer, they will determine the right method for your project.
Keeping these considerations in mind when designing a plastic molding ejection system can help your production run smoothly with little risk for cycle errors or part defects. An incorrect ejection system can lead to longer cycle times and lower the life of your mold. That’s why it’s important to partner with an expert plastic injection molding company like Midstate Mold. We run every stage of the injection molding process, from prototype design and testing and mold making to producing quality parts and quality assurance. If you require someone to tackle your next project, contact us today.