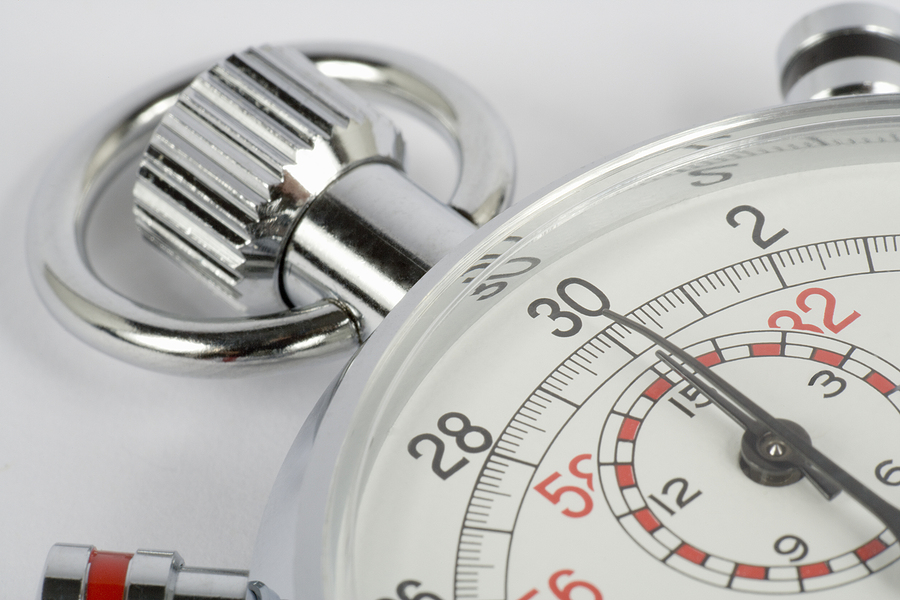
The increasingly competitive global workforce has challenged every industry. However, with new advancements in automation, machinery, and material handling, along with the innovative process known as Quick Response Manufacturing (QRM), plastic injection molders in the United States have been able to match overseas pricing. Not only that, but local manufacturers are even outpacing the competition in part design, execution, and lead times. Let’s discuss how manufacturers are exceeding their customers’ expectations by integrating QRM in plastic injection molding.
What is Quick Response Manufacturing?
QRM relies on a time-based framework designed to serve customers better and faster. Using shorter lead times to reduce cost, improve quality, and eliminate waste, injection molding manufacturers can swiftly provide their customers with the quantities of parts they need to improve cash flow while maintaining a lower inventory. It also reduces detrimental variability by employing strategies that limit rework and adhere to due dates. Companies have been using QRM to complement lean manufacturing strategies, making products in varying volumes to suit their needs and maximize profit.
How Do Manufacturers Exercise QRM in Plastic Injection Molding?
Logistical snafus throughout the pandemic and shipping bottlenecks over the past few years have done little to influence companies’ product demands. Businesses still require inventory despite logistical issues. That’s why the plastic injection molding industry has stepped up to reduce leads times by adopting the following strategies:
The Push-Pull System for Parts Manufacturing
As stated, QRM is all about timing: ensuring the client has the precise amount of product they need without encumbering inventory. At Midstate Mold, our push-pull system is dedicated to the premise of “just in time” manufacturing. By working with our client’s sales teams, we utilize their inventory predictions to determine when the next batch of plastic parts will be needed and how big that batch will be. This way, we have the right number of products ready to ship as soon as the call comes in.
Shortening the Supply Chain
A supply chain that includes overseas transportation isn’t reliable according to today’s standards. That’s why companies investing in local manufacturing are finding success. Locally sourcing resin ensures manufacturers have easy access to materials – not to mention domestic materials aren’t subject to sanctions and tariffs. Furthermore, domestic transportation ensures companies receive their orders on time. If your molds are held overseas, it’s far better to invest in tool relocation to adhere to the QRM process.
Calculating an Accurate Lead Time
At Midstate Mold, we have a comprehensive understanding of every component of the injection molding process that affects a production’s lead time. Among the most important are the design and processing phase, quality control, and delivery. Smaller, less complex parts are best when complying with QRM, but even when complex parts are produced – requiring closer inspections and higher machine maintenance – our employees are cross-trained so we can reallocate our staff where needed. Being a local manufacturer, we also don’t face the hurdles of international shipping, allowing for on-time delivery.
Operating a Turnkey Facility
Being a turnkey manufacturer means we handle all aspects of an injection molding project from beginning to end. There is a synergy between design and manufacturing, as our designers get to experience the plastic injection molding process on-site. Having one company handle an entire plastic injection molding project also drastically cuts back on lead times, meaning we can meet QRM requests that are especially time-sensitive.
Timeliness and strategy are vital when implementing QRM in plastic injection molding. That’s why it’s important that you work with an expert manufacturer with experience handling every step of the plastic injection molding process. At Midstate Mold, we’re early adopters of lean manufacturing, and we will perform everything from designing your part – including rapid prototyping – to running production and beyond. If you’re seeking a partner dedicated to your company’s success and maximizing profit, contact us today.