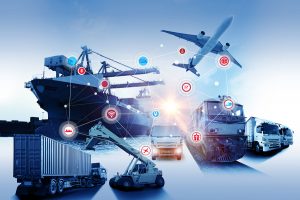
From production requests to manufacturing to shipping to distribution, plastic parts logistics are rarely straightforward, simple, or short. As a crucial link in that chain, we at Midstate Mold and Engineering have some insights on what you can do to protect your plastic parts supply chain from disaster, from dealing with delays and shortfalls to what to change if your supply chain is constantly breaking and affecting your bottom line. Read on to learn about the usual places for delays and what to do about them.
Finding Your Weakest Supply Chain Link
It’s time to analyze the various parts of your supply chain to find your potential bottlenecks or causes of constant delays. From top to bottom, let’s look at a typical supply chain for injection-molded plastic parts and where potential delays crop up.
Client Requests for New Parts
The supply chain starts when you request additional parts. Are you monitoring part usage and sales to forecast when you’ll need more parts? Do you have procedures to quickly put through parts requests? Check and make sure all parts of your company are talking to each other.
The Injection Molding Manufacturing
Once you send the request, it’s time for your manufacturer to take over in the plastic parts supply chain process. How is your relationship and process with them when it comes to new manufacturing? Make sure to talk to them about how they safeguard you from any delays.
Shipping Your Plastic Parts
Depending on the location of your manufacturer, your longest chain (and cause of the most delays) could be your shipping from the factory to you. If you’re looking at overseas shipping, it’s important to keep in mind all the delays that can occur from bad weather to bad trade relations between countries.
Troubleshooting Your Injection Molding Logistics
When it comes to dealing with potential delays and disasters, you’ve got two major choices. You can either shorten the supply chain by increasing the speed between points or reinforce the links by building in systems in support of lean manufacturing. Let’s look at two solutions to these problems.
- Tool Relocation: If your injection mold (tool) is located overseas from you, think about performing a tool relocation to bring down the delay between shipping and receiving. It’s just one of the perks of domestic manufacturing.
- The Push-Pull System: Another option is using the “push-pull” system, a type of agile manufacturing process that makes sure that your parts are ready to go the second you need them. Learn more about our system here.
If your manufacturer is unable to help you with delays – both regular and due to incidents – it might be time to look at working with someone who understands the need for lean and agile manufacturing. Midstate Mold and Engineering can help you analyze your needs and weakness, including the hidden costs of overseas manufacturing. Contact us today to learn more and request a quote so we can better understand your current needs and situation.