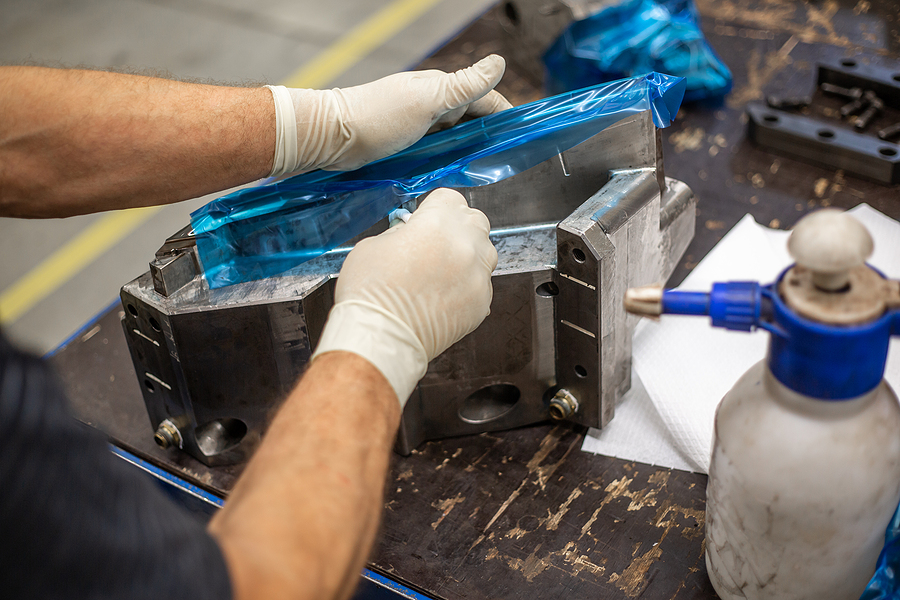
Manufacturing products entirely made in-house can seem like an attractive proposition, but it’s a prospect that is either extremely difficult to achieve or outright unattainable. It’s usually a consideration rooted in the perceived notion of reduced costs or faster production, but the likelihood of achieving either of these benefits is slim. In fact, outsourcing some of your product’s parts can have many immediate and long-term benefits that exceed in-house production. Let’s specifically review some of the advantages of sourcing your injection molding.
[Read more…] about The Advantages of Sourcing Your Injection Molding