There are many features for plastic parts that are best implemented through injection molding. Today, we’re looking at the “living hinge,” a specially designed bridge between two pieces that works like a traditional hinge, but without the need for using new material or assembly. Specifically optimized for injection molding, a living hinge is a great tool when it comes to optimizing parts for injection molding. Let’s look at how they work and common types to use in your next project. [Read more…] about Injection Molding Features: The Living Hinge
Should You Choose Plastic Injection Molding or Spin Casting?
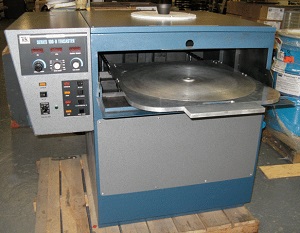
When it comes to producing your plastic parts, you’ve got several manufacturing processes to pick from. While we will always point to the advantages of injection molding, it’s important to understand the alternatives and which niche in the market they fill. Today we’re looking at spin casting and contrasting it to injection molding. Which is the best for you? It all depends on your needs and the scale of your project. [Read more…] about Should You Choose Plastic Injection Molding or Spin Casting?
The Importance of Gate Design and Gate Size in Injection Molding
While injection molds tools are hard to design and manufacture, their core concepts are easy to understand. The mold itself consists of two faces, between which is the cavity and core set into which the plastic is injected. The plastic – which, like its namesake implies, is injected into the mold through a sprue that feeds the runner plastic enters the mold’s cavity through the gate. The gate is the literal gateway of plastic into a cavity/core and therefore can make or break a mold. Too small and the mold cannot fill completely; too large and the plastic is too hard to shear. [Read more…] about The Importance of Gate Design and Gate Size in Injection Molding
Building a Plastic Injection Molding Tool for Success
It’s important to understand that the quality of the end product of injection molding – the plastic part – is a product of three major things: the plastics used in the injection process, the injection machines themselves, and the tool that casts the injected plastic into the final part. While all play a critical role, many of the issues that can arise from the project can be traced back to the molding tool. Time, cost, and the location where your tool is made can all affect the end product, which in turn can affect your end product. Learn what it takes to build the best plastic injection molding tool. [Read more…] about Building a Plastic Injection Molding Tool for Success
Advantages of Injection Molding Over Rotational Molding
If you are considering creating a plastic product, then you’ve asked yourself: What are the differences between injection molding and rotational molding? How do they compare in costs, production consistency, materials and design flexibility? We have discussed the advantages of the plastic injection molding process previously in our blog Five Advantages of Plastic Injection Molding. Before we examine the advantages of injection molding over rotational molding, we’ll need to examine the process of rotational molding. [Read more…] about Advantages of Injection Molding Over Rotational Molding
Fundamentals of Surface Finish in Injected Molded Parts
Once a part is molded, most plastic parts require additional processing for completion. Many plastics finishing processes are performed for appearances purposes or aesthetics, such as surface finishing. Surface finish can be used to give an injected molded part a certain look, feel, or texture. The surface finish can be a critical factor in either the appearance or performance of your product as it serves both a cosmetic and functional purpose. [Read more…] about Fundamentals of Surface Finish in Injected Molded Parts