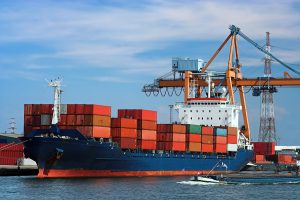
Cost is a critical part of every business’s manufacturing. While injection molding is one of the cheapest options for large-scale manufacturing of plastic parts, there are some considerations to account for before you move that manufacturing overseas. Today, we’re going to look at common design and production issues with offshore injection molding, including issues with mold and part quality, differing design and manufacturing standards, and localization issues.
Lower Quality: Assurance and Materials
Quality versus costs is one of the major tradeoffs for using offshore manufacturers. These choices, such as having your mold designed and built there, can have costly consequences for all downstream manufacturing that relies on that mold or parts.
- Lower Quality Molds: Molds are the most expensive part of the injection molding process, so offshore mold-making can save money at a cost. You may be missing critical design features or have a mold with a limited lifespan.
- Lower Material Selection: Typically, you’ll have a limited selection of injection molding resins to choose from, including lower-quality plastics, which not only significantly reduces the life of the mold but its safety, as well.
- Lower Quality Assurance: Lower overhead for manufacturers typically means lower quality assurance for machines, staff, and part defects, all of which means a higher chance of part failure.
Learn more in our blog, The Dangers of Using an Offshore Mold Maker.
Different Design and Manufacturing Standards
Different countries have different standards when it comes to manufacturing. Some can be to your advantage, such as lower labor and operations, but others can lead to design and manufacturing mismatches. Some standards, such as the QA standards mentioned above, are self-explanatory, but others can lead to final molds and parts that don’t meet your needs.
US vs. Offshore Manufacturers: De-molding
For example, the standards for de-molding (the removal of plastic parts from a mold) in China vs. the US are different. American manufacturers typically require automation of the de-molding process to avoid compromising the mold’s cavity while China does not.
Production Getting Lost in Translation
If your manufacturer’s native language is not English, you could have communication issues. This can include long delays in communication as both parties have to rely on third-party translation, but it doesn’t just interfere with day-to-day operations. If they are also helping you design and develop parts and their injection molds, these communication errors can lead to issues with these projects as well—potentially delaying production timelines or introducing costly miscommunicated design elements and expectations.
While this blog focuses on design and production issues that are common when working with offshore injection molding manufacturers, they aren’t your only consideration. Long transit times and an increasingly fragile logistic chain can lead to costly delays as well. To learn more about the perks of working with a US manufacturer for your mold and parts, contact Midstate Mold today. We can walk you through prototype development, create your mold on-site, and perform the production of high-quality parts.