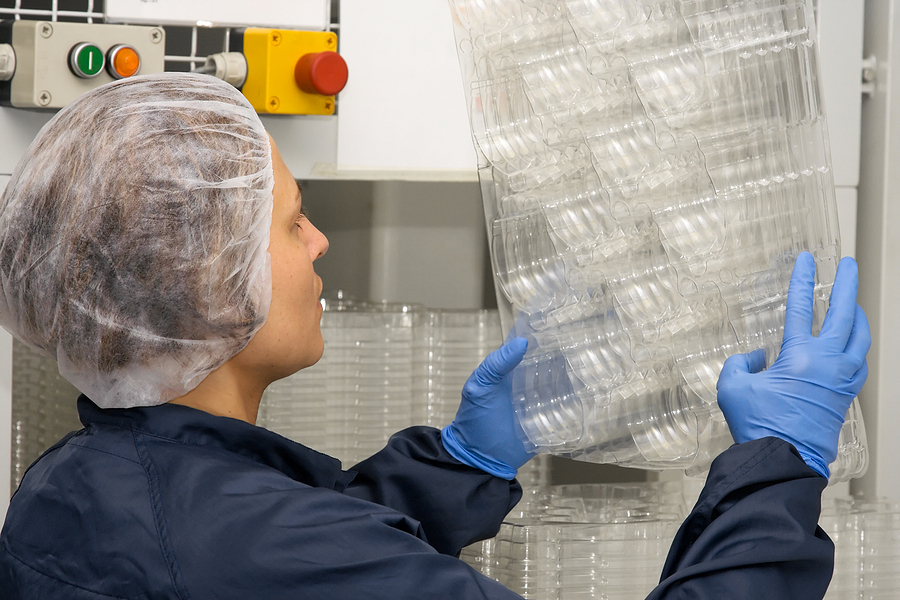
Using plastics in a wide variety of industries provides strength, versatility, and cost-efficiency that is difficult to achieve with many other materials. However, determining the application for which you intend to use plastics can inform you of the manufacturing process you should pursue. In particular, two popular methods for manufacturing plastic parts – plastic injection molding and thermoforming – offer many unique advantages depending on the specifications required for your project. In this blog, we will compare the advantages of both so you can determine the best option for you.
What Are the Advantages of Thermoforming?
Whereas injection molding uses a complex mold to shape the plastic, thermoforming is a single-sided fabrication process wherein a heated plastic sheet is formed over the surface of a mold using vacuum or air pressure. Once the plastic cools, it’s released from the mold, retaining the part’s shape. This simple yet efficient process has many unique advantages:
- Rapid Product Development: Thermoforming is faster than injection molding when it comes to development and prototyping plastic parts, as the molds are only single-sided, making the part and mold design easy to execute.
- Low Tooling Costs: Not only are thermoforming molds single-sided, but they also use a less-expensive aluminum than injection molding. This results in only requiring half the materials than a plastic injection mold.
- Large Variety of Color and Texture Options: The materials used in thermoforming allow for silk screening, printing, stenciling, and other coatings that can support unique textures, designs, and finishes.
- Easily Adjustable and Adaptable: While injection molding may be slightly more time-consuming when making adjustments to molds, thermoform molds are made with more ductile material that can be quickly modified at a lower cost.
These attributes are beneficial for large but simple parts such as product packaging, wall and ceiling panels, air ducts, and several other applications. It’s an ideal process for low production quantities.
What Are the Advantages of Injection Molding?
As opposed to thermoforming, injection molding often takes a bit more design and engineering time upfront, as the manufactured parts tend to be more complex. However, given the intricate process, it offers many distinct advantages:
- Cost Reduction Methods: While injection molding is generally more expensive than thermoforming, simplifying or streamlining the part design, simplifying the mold, or performing undercutting are just a few options available to drastically reduce the price per part.
- Low Scrap Rates: Trimming is a component of thermoforming that cuts away the excess plastic from the formed sheet, leaving a lot of plastic scraps that can’t be recycled. Injection molding uses precise measurements to avoid unnecessary waste and can even reuse recycled materials.
- Precision and Efficiency: Plastic injection molds are capable of executing complex and intricate parts that are incapable of being made by thermoforming. You can also expect high-quality parts with consistently accurate results.
- Greater Strength and Product Life: The parts created during injection molding are durable, as engineers can incorporate features that add structural strength.
Plastic injection molding is ideal for both low- and high-production manufacturing and has more options for size and complexity than thermoforming. It’s used in several industries to make parts such as medical diagnostic kits, aerospace components, and countless other products, and it can even take advantage of resin additives.
Plastic injection molding and thermoforming are popular manufacturing methods, and the choice of which to use for your production depends on your needs. If you’re looking for an inexpensive option for low or high production of complex, durable parts, plastic injection molding is your best bet. At Midstate Mold, we’ll walk you through our process – from prototyping your part to production – and determine whether our services are the right fit for your needs. If you’re interested in receiving a quote or wish to inquire more about our process, contact us today.