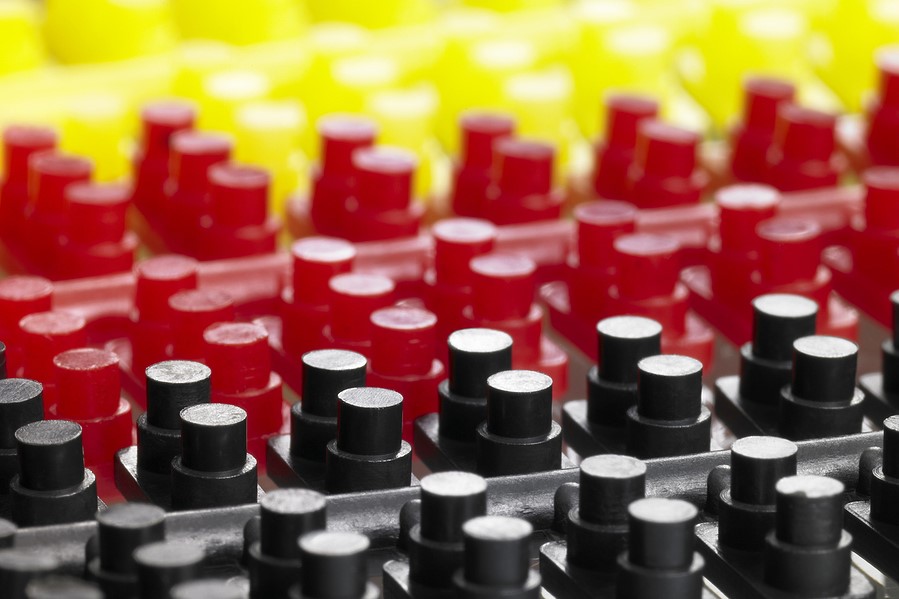
If you want your part’s appearance to pop, you’ve got several options and choices ahead of you. From high-quality finishes and textures on molds to changes in the plastics, additives, and manufacturing processes, there’s a lot to take in. Today we’re going to look at the two most common options: additives for coloring and finishes to the mold itself, along with other considerations, drawbacks, and options when it comes to injection molded parts.
Color Additives: Changing the Nature of Resin
The most common way of changing the color of plastic is an additive, a material that is compounded with the injection resin to change the nature of plastics. Changing color with these additives is common, such as using carbon black to make black plastics. It’s important to note that different additives can change aspects of your finished product, such as:
- Colorants: These are used to add color, special effects such as fluorescence, or patterns to products.
- Antimicrobial/Antiviral: Used to control the build-up of bacteria, fungi, algae, and viruses on the surface of food-related applications or high-contact consumer products.
- Antistatics: Used to decrease static electricity conduction and are often used in sensitive electronics and industrial goods.
- UV Stabilizers: Used to protect the resin’s mechanical properties by absorbing selective UV rays (less degradation).
- Plasticizers and Fibers: Plasticizers are used to make resins softer, more flexible, and pliable, whereas fibers add strength and stiffness.
- Flame Retardants: These are used to make products resistant to combustion or eliminate their tendency to burn.
- Optical Brighteners: Used to improve whiteness.
Multiple types of additives can be added, such as a colorant and glass fiber. Learn more in our blog, What Additive Applications Improve Resin Characteristics?
Mold Finishes: How Manufacturing Changes Aesthetics
If additives are about changing the nature of the resin, finishes are about changing the nature of the manufacturing process, typically starting at the mold level. These typically fall into one of two camps: adding a texture or buffing the mold to produce a textured finish or smoothness to the plastic or changing the manufacturing process, such as controlling injection speed and temperature. Faster injection speeds with higher temperatures (either heated molds or higher melt plastics) can produce glossier finishes. Learn more about this in our blog, Fundamentals of Surface Finish in Injected Molded Parts.
Other Design Considerations on Injection Molding
Of course, the surface appearance isn’t the only consideration. Additives and finishes can affect other properties of your plastics, and other properties can affect appearance. Also, keep in mind that some changes may affect others, like certain additives causing a rougher finish, so it’s essential to consult with your manufacturer first.
- Mold Health and QA to Avoid Defects: Making sure a mold is in good condition and being properly used, along with rigorous QA, is vital to avoid part defects that affect appearance.
- Better Finishes Promote Paint and Sticker Adhesion: A textured finish can provide a better grip, including for any paint or stickers for the final product.
- Considerations Depending on Different Fields: Depending on the field your part is designed for, certain colors or qualities might be preferred, such as high-vis or anti-microbial.
Working with a skilled plastic injection molder will help you make the right decision on the appearance and finish of your product, but it’s important to start this work early with part prototyping to make sure you’ve got the right designs and mold quality. As mold makers, maintainers, and manufacturers here at Midstate Mold, we’re ready to talk to you about your needs. Contact us today to get started or dive right into a quote.