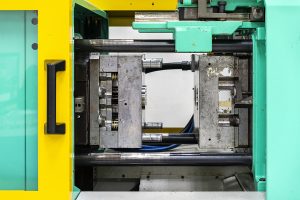
A lot of work goes into designing injection molding parts and the molds that produce them. While there are a thousand considerations to keep in mind with parts, molds, and manufacturers, today we’re going to focus on three: gates, pins, and parting lines. Designing parts and molds for those parts with placement for these features in mind produces better results and underlines why collaboration with your manufacturer earlier in the process can help avoid costly redesigns or inefficient production later.
1. The Importance of Gate Design & Placement
A gate is the location where molten polymer enters the mold. There are multiple part and mold design considerations when thinking about the placement of gates, their size, and number.
- Gate Placement: Depending on the design of the part, different placements make more sense. For example, for a long and narrow part, gate placement makes more sense at one end than a central location for a rounded part.
- Number of Gates: While all molds have at least one gate, most designs have at least two or more gates. The number of gates, balanced with placement and size (see below), allows molds to be filled efficiently.
- Size of Gates: The gauge of the gates is also important. While small gates may provide a nicer appearance to the part, they can take more time or pressure to fill. This can lead to mold stress that wouldn’t happen with a larger gate.
For more information on gates and gate design, make sure to check out our blog, The Importance of Gate Design and Gate Size in Injection Molding.
2. Ejector Pins Design to Minimize Impact
Once a part is injected into the mold and cooled, ejector pins in the mold force out the completed part. Ejector pin locations are often overlooked by part designers, but the indentations and marks they leave on parts indicate the required amount of force and positions. Knowing this information early on is essential to the quality of the final part. Often times, this works best in collaboration with the mold and part manufacturers as rapid part prototyping before the part is finalized and the mold created.
3. Designing Parts Around Parting Lines
When you’ve got more complex parts and parts where the surface finish is important, it’s worth stepping back to design around your parting lines, where the two sides of your mold meet. And it’s not just cosmetic: very complex parts may not have parting lines that are possible without going back to the design board.
Using CAD for Better Mold and Part Design
It’s worth working with a mold manufacturer who employs the advanced features of CAD software (such as SolidWorks CAD) so flow analysis and other thermoplastic properties can be taken into consideration for part orientation to provide the best placement for parting lines.
Keeping these considerations in mind when designing parts can help your production run smoothly with little risk of cycle errors or part defects. That’s why partnering with an expert plastic injection molding company like Midstate Mold is vital. We run every stage of the injection molding process, from prototype design and testing and mold making to producing quality parts and quality assurance. If you require someone to tackle your next project, contact us today.