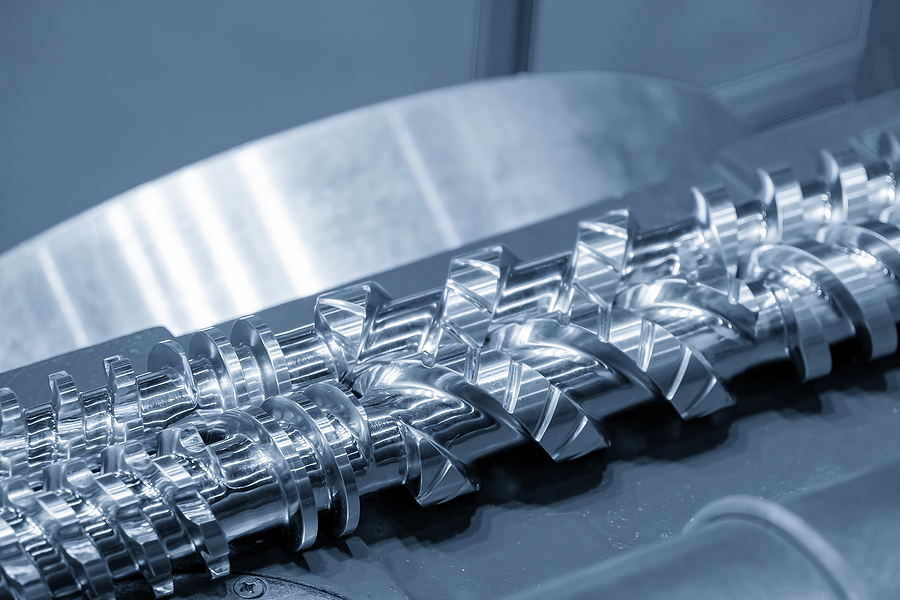
Experienced manufacturers are aware that certain conditions in the injection molding process have a large bearing on the properties of the final product. Two important elements in the process that weighs heavily upon a part’s performance requirements are proper melt and mold temperatures. In order to truly appreciate the collaboration of these two stages and how they produce higher qualities parts at a lower cost, let’s take a look at how melt and mold temperatures cooperate to form a final product.
How Is the Melt Temperature Achieved?
The melt temperature refers to the temperature of the polymer as it passes through the nozzle and hot runner and into the mold. In order to determine an ideal melting temperature, the type of thermoplastic, residence time, the screw and barrel assembly, and the requirements of the final product must be accounted for. Based on these variables, the barrel setpoints are adjusted by the manufacturer to heat the resin to the desired melting point.
How Does Melt Temperature Affect the Final Product?
The melt temperature can affect the viscosity of the plastic and the final product’s molecular weight, and if the melt temperature is inconsistent or is not uniform during injection, it can result in part defects. Furthermore, the melt temperature can be adjusted to affect the properties of a part. For example, if you slightly decrease the melt temperature of certain resins, such as polypropylene, the finished product will have higher impact resistance, a shorter mold cycle time, and the molding process will consume less energy.
How is the Mold Temperature Achieved and What’s Its Purpose?
A lesser-known process but an element that perhaps has a more profound effect on the final product is the mold temperature. For this process, the surface of the mold is heated, maintaining the liquid state of the plastic, offering less flow resistance, and creating pressure in the cavity. It is also a major contributor to the cooling process as it controls the rate at which the final product solidifies. Similar to the melt temperature, the mold temperature is calculated with the part design, geometry, surface finish, residual, and shrinkage in mind.
How Does the Mold Temperature Affect the Final Product?
If improperly managed, the mold temperature can result in part defects – such as sink marks, discoloration, and warping – as well as ejection or jetting defects. However, when properly calculated, the mold temperature can affect the properties of the final product by offering resistance to stress and wear, altering the molecular weight, and providing uniform stability.
How Do Melt and Mold Temperatures Work Together to Achieve a Goal?
For plastic injection molders, calculating the ideal melt and mold temperatures is pivotal to achieving optimal part performance. For most resins, the melt is lower than the mold temperature, which acts together to streamline the cycle time, reduce costs, and generate a sturdy and reliable product. Inexperienced molders may see higher melt temperatures as a means to reducing resin viscosity and increasing production. If these two elements are not working in conjunction with one another, they can lead to resin degradation, increased energy consumption, and prolonged cooling times.
It’s important for a manufacturer to understand how melt and mold temperatures cooperate to form a final product because this process plays a large role in determining the integrity of the part, the lead time, and the overall costs. When you’re searching for a manufacturer, it’s important to ensure they have in-depth knowledge of each step of the plastic injection molding process. At Midstate Mold, we’re a turnkey manufacturer with over 55 years in the business, helping clients with everything from prototype development to production. If you need an experienced partner, contact us today.