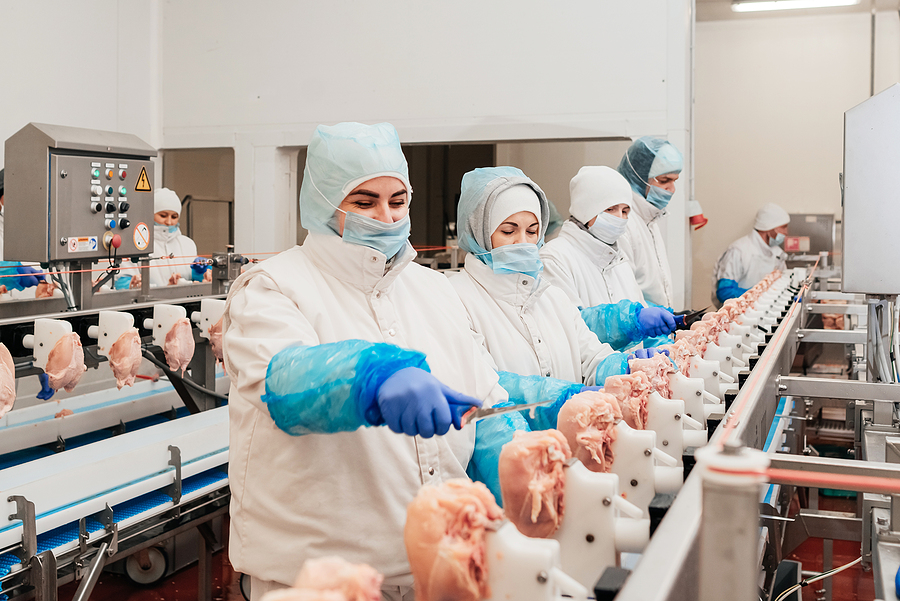
When visiting the market, you can trust plastic containers to keep the shelves stocked with fresh foods. Not only do plastics preserve food for consumption, but they’re also used in the production process. What’s important to understand about these plastics is that they’re comprised of food-grade variants, making them safe for use in the industry. So much of what goes into making food available to the public relies on plastic injection molding. If you’re looking to use food-safe plastics for your next project, you may want to learn how plastic injection molding revolutionized the food and beverage industry.
The Efficiency and Fast Production of Plastic Injection Molding
Plastic injection molding has the capacity for high-volume production using technology that is highly efficient. It has the capability of keeping up with the fast-paced food and beverage (F&B) industry due to its rapid output rate. This method is also more cost-effective than most other processes, so it helps F&B companies generate higher revenue and profit margins while charging less for their product.
Diversity of Food and Beverage Applications
The industry requires a wide range of diverse applications when it comes to both packaging and processing the products. Fortunately, the food-grade thermoplastics available in injection molding can safely produce caps and transparent containers and parts used in food-processing machinery. Manufacturers are capable of creating temperature-resistant plastic containers for storage and serving hot foods and beverages. Impact- and friction-resistant polymers can also provide crucial components used in the F&B manufacturing process.
Complex Injection Molding Parts Designs
Containers and equipment in the industry require complex designs such as undercuts for clasping mechanisms. Fortunately for injection molding manufacturers, they have the tools to create and handle highly complex plastic parts while performing quality control to ensure uniformity throughout production. The plastic injection molding process can be trusted to create a high volume of identical parts with little to no compromised quality. In the F&B, consistency is essential to preserve the end product and keep consumers safe.
Freedom of Choice in Material and Color
A factor that is incredibly valuable in the F&B industry is the ability to incorporate different colors and materials in product packaging. Injection molding grants you the advantage of selecting from a variety of color additives and materials so that the contents of the end product remain safe for consumption while simultaneously standing out. Working with the right manufacturer, they’ll be able to meet your specifications while remaining in compliance with the Food & Drug Administration and other industry safety regulations.
Enhanced Strength for the Food and Beverage Industry
Plastic is capable of being rigid or flexible, with a strength factor that suits the needs of the product. When designing a part based on how it will be used by the consumer and the environments it will be exposed to, it’s important to ensure remnants of the packaging don’t compromise the product. With food-grade variants that feature high tensile strength, you don’t have to worry about consumers ingesting harmful materials.
By taking a look at the ways plastic injection molding revolutionized the food and beverage industry, it’s easy to see that plastics are the best material for ensuring safety. The cost-effectiveness and fast production times also help pass on savings to consumers. At Midstate Mold, we have experience designing prototypes and providing manufacturing for the food and beverage industry along with many other fields. If you require the help of an experienced manufacturer to tackle your next project, contact us today.