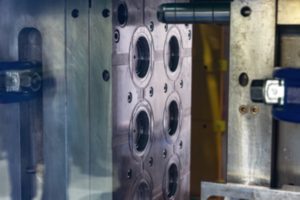
Every manufacturing process can introduce different defects into the final product. The goal of every manufacturer is to have the machines, process, and quality assurance in place to reduce and even remove flaws from final parts and products. Welcome to another blog on defects and how to detect and troubleshoot them. This week we look at jetting defects in plastic injection molding. Let’s go over what they are, how they are caused, and what injection molding companies do to avoid them.
Identifying Jetting Defects in Injection Molding
Jetting is a defect that’s very clear to the naked eye, with a serpentine spray line visible on the surface of a plastic part, which is why it has earned the nickname “worm tracks” for its similarity to the slime trails of worms or snails. However, unlike a molding defect such as splay, which is largely a cosmetic defect only, jetting shows a serious problem with the injection molding process, as this molding defect undermines the structural integrity of the part due to what causes jetting in the first place.
What Does Jetting Do to a Plastic Part?
Jetting occurs when the melted plastic (known as the “melt”) is injected too fast through a restive area (such as a gate, nozzle, or runner) into an open cavity in the mold without first forming contact with the mold wall. The melted polymer sprays into this cavity with this characteristic back and forth snake-like motion before the mold starts to fill normally around it. The issue is that this initial jet of plastic has already started to cool as the mold fills up around it, this temperature difference meaning the two flows of plastic don’t fuse, causing the defect we know as jetting.
Troubleshooting Jetting in Plastic Parts
There are three major sources of jetting defects: issues with how plastic flows into the mold, the speed of the plastic entering the mold, or the temperature of the plastic.
- Improper Gate Placement: An improperly made (or thought-out) injection mold may have a gate placed to inject directly into the center of the cavity, which can cause this problem. The gate may need to be moved or reconfigured to provide the flow needed (such as expanding the gate diameter).
- Injection Speed is Too High: The issue may also not be with the mold but the injection machine. The speed in which the plastic is injected into the mold (known as the ram speed) may be too high. The inject speed needs to be reduced on the molding machine.
- The Plastic is Cooling Too Quickly: The presence of jetting might mean you have another issue: plastic is cooling too quickly within the mold. You might need to look at using hot runners with mold or having a heated mold. Alternatively, you can look at using a different plastic.
For more on changes that need to be made to injection molds, check out our blogs, Building a Plastic Injection Molding Tool for Success and The Importance of Gate Design and Gate Size in Injection Molding.
Avoiding these and other injection molding defects is all about using the right mold manufacturer and having a part manufacturer that has the right quality assurance to catch these defects and troubleshoot them. If you’re interested in working with someone who does both, it’s time to contact Midstate Mold & Engineering. Interested in reading up on more part defects? Check out part one and part two of our Uncovering Molding Defects and How To Troubleshoot series.