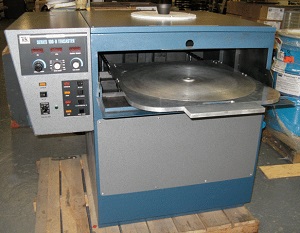
When it comes to producing your plastic parts, you’ve got several manufacturing processes to pick from. While we will always point to the advantages of injection molding, it’s important to understand the alternatives and which niche in the market they fill. Today we’re looking at spin casting and contrasting it to injection molding. Which is the best for you? It all depends on your needs and the scale of your project.
The Basics of Plastic Injection Molding
Plastic injection molding produces parts by injecting molten materials – most commonly thermoplastics – into molds, also known as tools. Before being injected, the plastic is heated in the barrel, injected into the mold, moves along channels known as runners, and then into the part itself. Once completed, the mold opens, and the part is ejected, ready to start the process again. Loaded into hydraulic or electric machines, a well-made mold, and the right plastic resin can produce precision parts at a very fast rate.
Plastic Injection Molding: High Capacity with a Cost
This all comes together because of a long startup process of designing and making the mold, and the cost associated with it. Some things to keep in mind:
- Fast and Efficient: Depending on the complexity of the mold and material selected, the mold can easily produce 1000s of parts per day, on machines that are largely automated which reduces overall production costs.
- Flexible and Lean: Injection molding can make complex parts because of the high pressure it can exert on a mold. On a well-designed mold, little plastic is wasted. Depending on the plastic used, the excess can be recycled back into the process.
The Basics of Spin Casting
Spin casting uses two things: a cast of the part and centrifugal force from spinning. A cast of the object is made, either using silicone or rubber, usually by pouring molten versions directly onto the product. After becoming solid, the resulting mold is cleaned before being vulcanized to harden the material before it is gated and vented and ready for the spin caster machine. The machine is essentially a large motor and clamp for the mold, spinning the mold up while the material, usually thermoset plastics, is poured into the top of the mold to spread throughout the object.
Spin Casting Features: Low Run, Low Volume, Low Price
The major advantage of spin casting is the speed of setup and lower startup price at the cost of the speed and lifetime of production. A few points to keep in mind:
- Soft Molds: While spin casting molds can be created relatively quickly and for low costs, they are also much more fragile than steel tool molds. This translate into much fewer production cycles before the mold breaks down, on a scale of 100s instead of 1000s from injection molding.
- Slow Cycles: The whole spin casting cycle is slow (though still faster than 3D printing), with it taking 30 seconds to several minutes depending on the material used, meaning a much lower volume of parts can be made in any given time.
Make sure to check out our blog on the similar process, rotational molding.
Picking the Right Manufacturing Method
When it comes to picking the right manufacturing process for your plastic parts between spin casting and plastic injection molding, it’s all about your needs. While spin casting produces small batches of parts quickly with less overhead, injection molding will always trump for projects with high scale and volume. Check out our blog, Is Plastic Injection Molding the Right Process for You? for more details, and contact Midstate Mold to learn more about the process and how it can be used for your product.