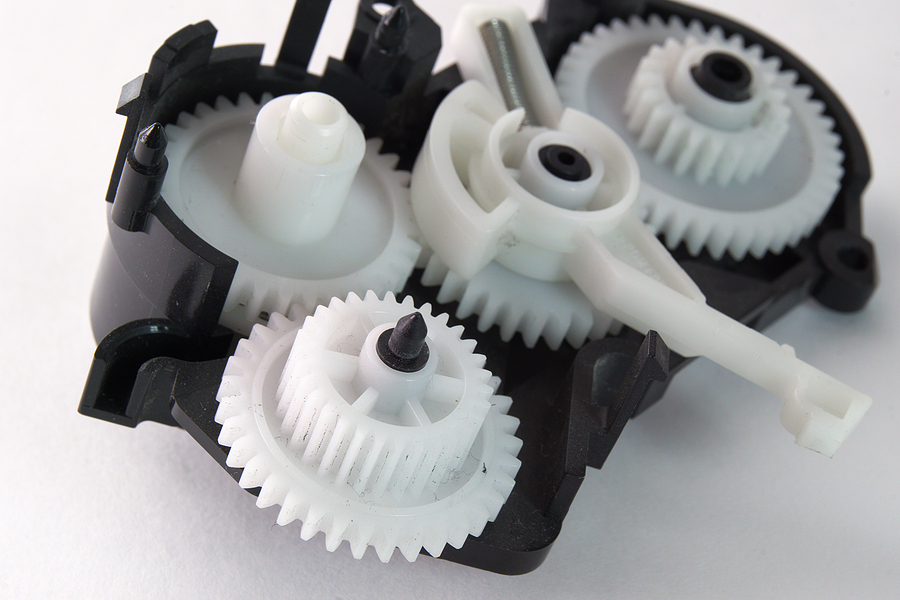
Injection molding is the most common manufacturing process, and businesses are eager to start projects using affordable and durable polymers. However, due to the intricacies involved in plastic injection molding, engineers need to carefully consider how they design their parts to ensure maximum part performance and reduced tooling costs. When a business’s engineers take it upon themselves to make an injection mold without the consultation of injection molding specialists, errors are sure to arise. Let’s review three of the common mistakes in designing products for injection molding.
1. Lack of Collaboration with Vendors
Businesses that heed the advice of their manufacturing vendor too late in the design process run the risk of a low-quality end product and high production costs. While it may appear you have the scope of the project realized before involving the manufacturer, businesses that bypass collaboration place too much focus on the end-user of the part and none on the manufacturing process. When you work early with your vendor, the injection molding engineers will help you build a more efficient part that can be machined with a limited risk of setbacks. It can also protect you from costly tool redesign.
2. Bypassing the Prototype Phase
While some suspect prototyping is just an extra, unnecessary step in the injection molding process, skipping this step can lead to production line disruptions and loss of time and money. Manufacturers essentially use prototype tooling as a learning tool. They use a prototype mold for the following purposes:
- Test Polymers: The performance of the plastics being considered can be tested during this phase, and the part can be assessed before committing to mass production.
- Confirm Geometry: During the prototyping phase, you can root out potential defects in the part design. The viability of complex design elements, like undercuts, can be confirmed.
- Assess Gate Locations: Prototype tools allow the manufacturer to apply cuts and welds to adjust the gate locations. Doing so to the final tool will limit its lifespan and add time and costs to production.
Some manufacturers like Midstate Mold can even use a method referred to as rapid part prototyping, which uses computer-aided design (CAD) software to create a scale model of a plastic part. This helps in accelerating the time between prototyping and production.
3. Overlooking Key Design Elements
Inexperienced vendors or businesses performing their own part design may not be knowledgeable about aspects that could influence the final product. With the help of an experienced injection molding manufacturer, you can accurately determine design elements such as:
- Materials and Wall Thickness: By determining the part’s intended applications and the flexibility of the plastic, a manufacturer can incorporate a wall thickness to certify longevity and durability.
- Draft Angles and Radiused Edges: These are slants and curvatures in a design that attribute to the separation of the plastic from the mold. To avoid friction damaging a part during ejection, an experienced engineer with creating a mold with angled and rounded edges.
- Solid or Shell Parts: Parts will shrink during the cooling process. A manufacturer will be able to determine if a shell of the original shape is needed to prevent warpage from occurring.
It’s important these elements are carefully considered during the design phase, as discovering an error mid-production can be a significant waste of time and money. Tool redesigns are very costly.
Aside from these few mistakes in designing products for injection molding, there are even more problems that can arise if you try to complete a design without the input of your manufacturer. Taking it upon yourself to design a part is not worth running the risks of production delays and part defects. At Midstate Mold, our team will work with you on finalizing a suitable part design, with both your budget and requirements in mind, and perform both prototyping and production phases. If you need the help of an expert injection molding manufacturer, contact us today.