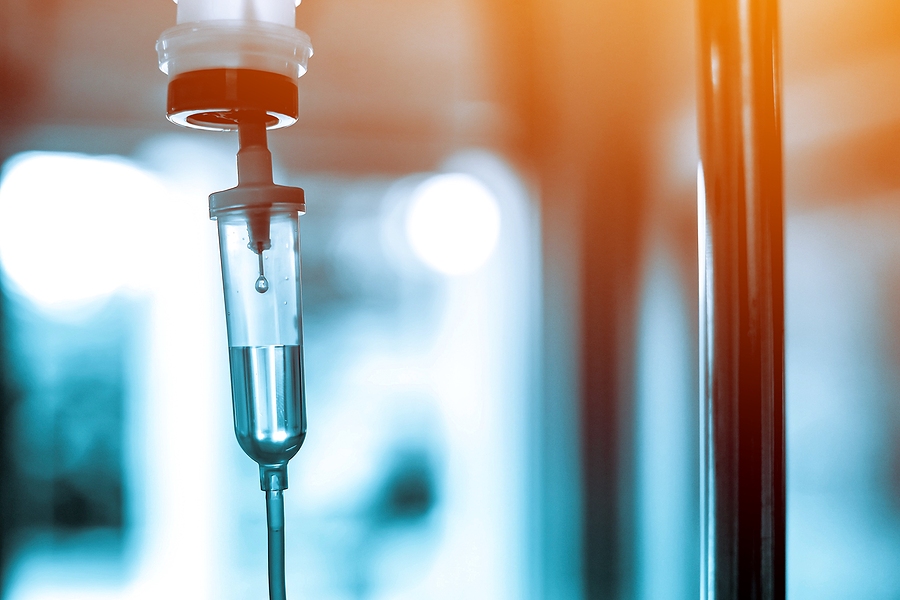
In times of COVID-19, medical plastics have never been in such high demand. From syringes to face shields, the plastic injection molding industry has had its hands full. Since medical utensils and devices are essential for performing life-saving tasks, not only do they require complex designs and functionality, but they also need to withstand a variety of medical environments, many of which include harsh chemicals and sanitation. To understand the safety precautions applied to injection molding, let’s take a look at the benefits of chemical-resistant resins in medical plastics.
Why Must Medical Plastics Be Chemical-Resistant?
In order to develop safe medical implementations, manufacturers select appropriate resins based on characteristics such as durability, thermal and electric resistance, and chemical resistance. There are many situations in the medical industry where devices and equipment may be subject to hazardous chemicals, sterility, high stress, and destructive microbes. Therefore, in order to maintain the integrity of the medical instrument, the Food and Drug Administration dictates that these plastics be created with chemical-resistant resins.
What Are Chemical-Resistant Resins Used in The Medical Industry?
Chemical resistance is such a valuable characteristic of medical applications because it keeps the other necessary properties of the plastic intact. While there are thousands of types of resins, only a few fulfill this criterion, such as:
- Polyetheretherketone (PEEK): PEEK is an organic thermoplastic with excellent chemical resistance. It is also safe for the human body, can withstand CT, X-ray, and MRI scanning, and can be sterilized using steam, electron beams, and gamma radiation.
- Udel Polysulfone: This resin is often used as an alternative to glass and stainless steel in medical devices. It boasts high durability and long-term resistance to chemicals, hydrolysis, mineral acids, salt solutions, and oxidation.
- Medical Grade Ultem: This resin is perfect for medical applications where methods of sterilization vary. It has a strong resistance to disinfectants, environmental influence, lipids, and UV and gamma radiation. It can be strengthened using glass additives to increase rigidity.
- Makrolon Polycarbonate: This plastic is lightweight and nearly transparent, with chemical-resistant and durable properties. Like the other medical plastics, they can be sterilized using extreme methods, such as gamma radiation and Ethylene oxide.
There are other polycarbonates, polypropylenes, and polyethylenes that have chemical resistance, as well, and plastic has been replacing many other materials in healthcare due to its durability, versatility, and customizable properties.
Use of Antimicrobial and Antiviral Additives in Medical Plastics
In addition to chemical resistance, the longevity of thermoplastics in the medical field can be increased with antimicrobial and antiviral additives. Including these additives in medical applications minimizes the presence of plastic-degrading bacteria, thereby protecting it from other sources of corrosion. It also increases the hygienic properties of the plastic, as not only will the chemical resistance allow the device to be sterilized, but the antimicrobial and antiviral additives will reduce other organic hazards. Chemical-resistant thermoplastics with additives are growing in popularity in the medical field due to the reusability and cost-effective nature of these materials.
Chemical-resistant resins in medical plastics are essential to creating reusable and sustainable devices. They allow engineers to develop creative solutions which are more environmentally friendly and safe to use during patient procedures. At Midstate Mold, we’re familiar with the ins and outs of the medical field and have experience with everything from prototype development to production. If your next project requires a complex medical design featuring chemical-resistant plastics, contact us today.