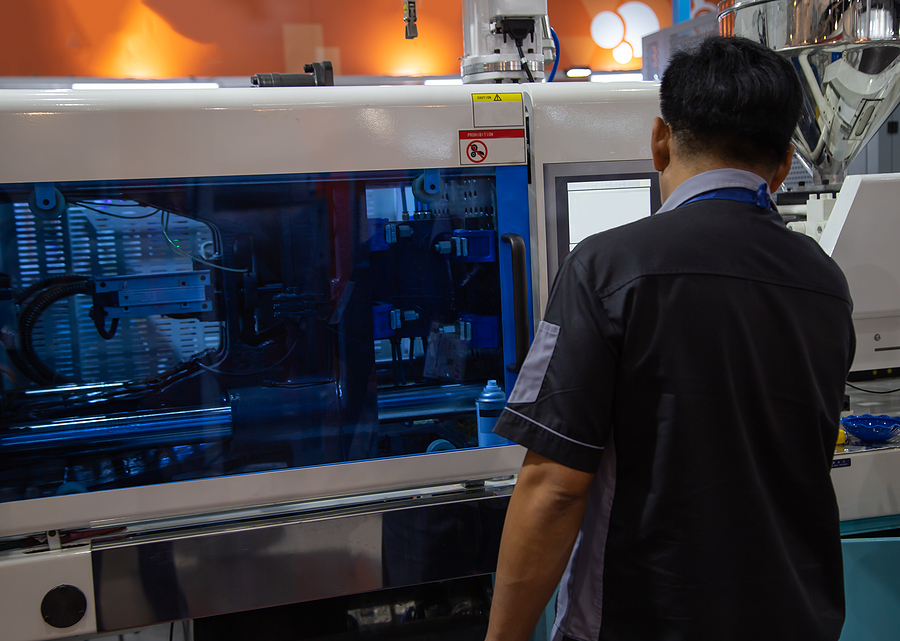
The more parts you produce in a given time, the lower your costs. While the injection molding cycle time is a major contributor to the overall performance of the bottom line of your company, it’s a process that should not be rushed. One integral component of injection molding – and one that takes up most of the cycle time – is cooling time. It has a major bearing on the quality of your final product, and it’s not an area where you can cut corners. In this blog, we’ll further dissect the importance of proper cooling time in plastic injection molding.
What Factors are Involved in the Cooling Process?
Before discussing the importance of cooling time, let’s take a look at what the process entails. An incredibly high temperature is required to melt plastic resin for injection, and due to this immense heat, the cooling process can take up to four-fifths of the cycle time, if not longer. The following elements of plastic injection molding are the temperature changing stages that lead up to the final product:
- Resin Heating and Injection: The base resin is liquified by being subjected to high temperatures, and once melted to the appropriate viscosity, it’s injected into the mold.
- Mold Packing and Holding: As the injection continues, some of the plastic begins to cool and shrink. To ensure the cavity is filled, additional material is injected and “held” to prevent backflow.
- Cooling Stage: The cooling process begins after packing and holding the material in the mold. During this stage, the plastic solidifies, taking on the permanent shape of the mold.
After this process, the part is ejected from the mold and inspected for quality assurance purposes. If cooling time is improperly calculated, it can result in defects.
Why is Cooling Time Important?
When cooling is improperly executed, the plastic part won’t sufficiently harden, leading to damage from the firing ejector pins. Even a mold’s design can influence the cooling process, resulting in increased shrinking, sinking, discoloration, warping, and delamination. If cooling channels are implemented into the mold’s design, it can aid in the dispersal of heat and lower the cavity wall’s temperature, which in turn leads to even cooling. However, excessive cooling can also result in an unnecessarily extensive cycle time, which is why it’s crucial molding manufacturers are capable of accurately estimating cooling time.
How is Cooling Time Calculated in Plastic Injection Molding?
Cooling time can be calculated by using an equation that incorporates wall thickness and a measurement known as thermal diffusivity – which quantifies the plastic’s thermal conductivity, density, and energy requirements to raise its temperature. The estimated time also depends on the type of thermoplastic, as each has different melting and molding temperatures. This is a complicated equation, but if you’re working with an experienced injection molding partner, they will be well-versed in this process.
Despite taking up the majority of the cycle time, cooling time in plastic injection molding should not be rushed. It takes a combination of patience, mold design, and accurate mathematics to generate a cooling time that will result in maximized manufacturing speed. Midstate Mold is an expert turnkey manufacturer that excels at creating prototypes and executing production, resulting in efficient lead times. If you would like to discuss our process and how we calculate every stage of our injection molding, contact us today.