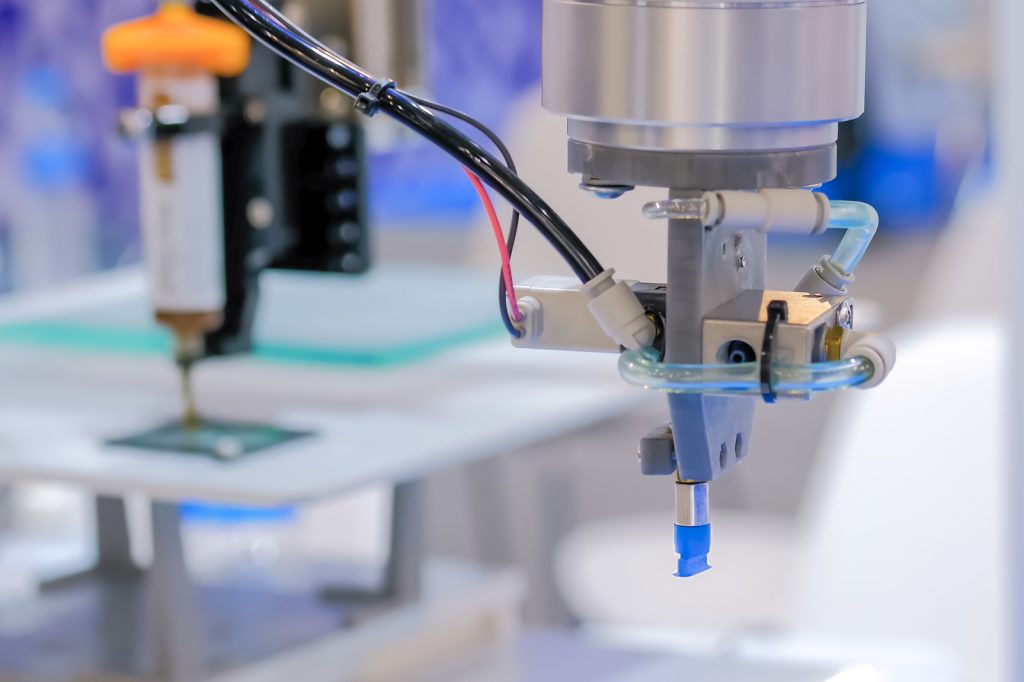
Robotics and manufacturing go way back to the start of the third industrial revolution. And while you may think of the automotive or computer manufacturing industries as the sole users, we’re seeing it more and more in other manufacturing sectors. Today, we’re exploring the new generation of robot “pick-and-place” systems and utilizing robotics in the plastic injection molding industry, including here at Midstate Mold & Engineering.
Robotics and the Manufacturing Industry
When you think about robotics in manufacturing, you’re probably thinking about robot arms assembling a vehicle or welding a component. Although robotics are nothing new in the assembly line, how they are being utilized today is different. Instead of assembly lines built around robotics, robotics are being introduced into existing systems or even single-stage manufacturing in the form of pick-and-place systems—bridging gaps that free up skilled workers for elsewhere in the manufacturing process.
Types of Pick-and-Place Robotics Systems
There are generally four major types of robotic systems for pick-and-place systems—that is, robots that are designed to pick up an object and place it in another location. Some systems can be further divided, such as “fast pick” systems that are designed for medium and high-volume manufacturing.
- Robotic Arms: Typically with a five- or six-axis system, robotic arms are what probably come to mind when you think robotics. These are perfect for standard pick-and-place applications, including flat planes and where placement isn’t exacting.
- Cartesian: Looking more like a gantry than an arm, cartesian robots function on the three axes (X, Y & Z) that give the robot its name. These provide higher accuracy than standard robotic arms but are more space and budget-efficient than other options.
- Delta Robots: When placement needs to be exacting, the multi-armed (usually three) deltas come into play, with advanced recognition and placement systems for assembly lines where placement is critical.
- Collaborative/Assisting Robots: Sometimes known as “cobots,” these systems are designed to work with a human counterpart. They might assist workers through assembly stages or work in tandem as guides.
Robotics Used at Midstate Mold
We’ve recently added two Yushjin YD Series Robots to our manufacturing line-up, pick-and-place cartesian systems focused on take-out operations using a rigid Carbon Fiber Reinforced Polymer (CFRP) gantry arm and vacuum hand for retrieval. They are being used for cavity separation and family mold part separation, helping eliminate manual labor for more consistent cycles so our skilled technicians can focus on other machines and areas, like quality assurance.
Check out the video below (or use this link) to see one in action!
Benefits of Utilizing Robotics in Plastic Injection
The application of pick-and-place robots and other robotic systems in plastic injection molding is almost endless. Some of the most common uses and benefits are:
- Mold Machine Tending: Pick-and-place machines can unload molded parts, freeing up an operator from this repetitive task for more complex work.
- Insert/Double-Shot/Overmolding: When it comes to processes where a component is inserted into a mold to produce a composite part, robots can provide more consistent results.
- Assembly & Post Processing: Robots can also be helpful in last-stage parts manufacturing, such as assembling parts or post-process cleanup.
- Thermoplastic Recycling: Pick-and-place robots can also more effectively gather up waste plastic that can be recycled, making for more efficient and green manufacturing.
Midstate Mold & Engineering is plastic injection molding done right, from being a US mold maker and manufacturer who exclusively uses recyclable thermoplastics to implementing the latest in machinery, robotics, and Industry 4.0 learning programs and AI. We have over 180 years of experience in both mold making and manufacturing, including exacting industries such as medical and life sciences. Contact us to learn how we (and our robots) can help.