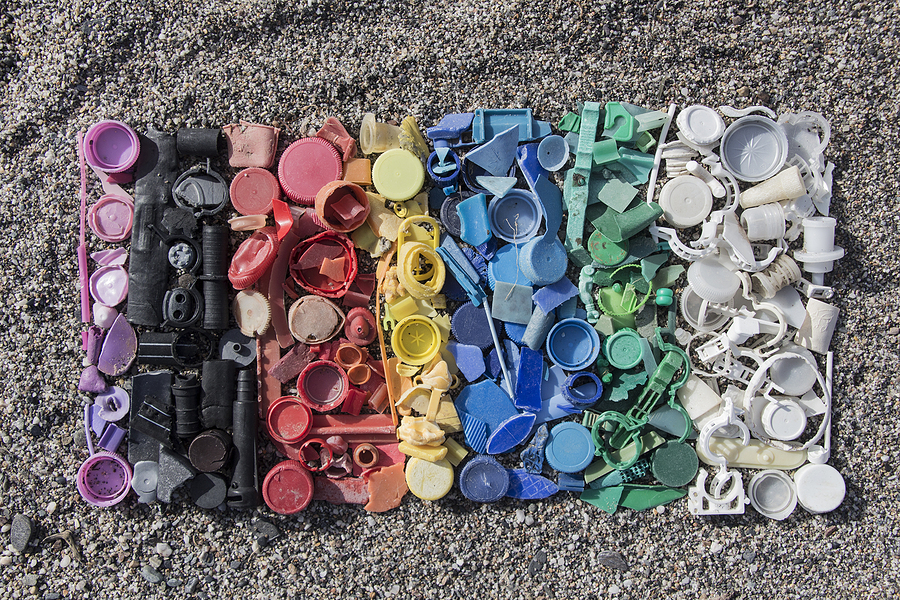
Discoloration in injection molding is defined as a disparity in the original color of the plastic. This part defect can arise from a multitude of sources, such as overheating, contamination, or manufacturing error. This inconsistency in the part’s coloring is caused by thermal degradation, and depending on the severity, it can influence how noticeable this defect is. In order to avoid this complication, one must first understand what can cause discoloration in plastic injection molding.
Injection Molding Machine Issues
There are several causes of discoloration that can arise from the injection molding machines. The simplest cause can be contamination resulting from equipment that has not been properly cleaned, resulting in dust contaminating the resin, but some other common culprits include:
- High Barrel or Nozzle Temperature: If the temperature of the barrel or nozzle is too high, the plastic overheats, resulting in thermal degradation that darkens the color. Reducing the barrel or nozzle temperature to the recommended range of the plastic can resolve this issue.
- Excessive Shot Size: If you exceed the recommended shot size, the plastic will require additional residence time in the barrel to prepare for injection. The plastic is then exposed to an extended period of heat, which also leads to thermal degradation.
- Prolonged Cycle Time: This issue can arise from a machine error or the operator causing some sort of delay or inconsistent cycle. If the cycle time is too long, the plastic can degrade and discolor in the heating cylinder.
The machine’s build can also cause injection molding defects. If there are components of the original injection molding tool that aren’t outfitted for extreme temperatures, such as an inadequate screw design, it can cause discoloration.
Problems with the Injection Mold
Discoloration arising from the mold has to do with temperature regulation. If a mold is hot, it compacts the plastic molecules before they solidify. This causes the part to be denser, resulting in a darker color in some areas. Additionally, if the cooling process is impaired in any way – such as an obstructed water line – it can cause the mold to overheat, causing thermal degradation. Alternatively, if there’s excessive cooling in one area, the material can become lighter in color. These issues can be rectified by adjusting the mold temperature according to the resin manufacturer’s recommendations.
Defects in the Thermoplastic
Sometimes discoloration can be a result of the raw materials. Mixing different grades of the same material or different flow values of the same material can result in color streaks, but other causes can include:
- Contamination: If the resin contains any contamination – whether from dust or dirt regrind – the plastic will undergo discoloration according to the type of contaminant.
- Moisture: The presence of excessive moisture or organic compounds can not only cause discoloration, but it can also result in pockets of air and weaken the plastic part.
- Decomposed Coloring Additives: If coloring agents are being added to the resin, discoloration can occur if the additives have become decomposed or were poorly stored.
The solution to these issues comes down to keeping the plastics dry, properly maintaining additives, and storing resin in secure containers that are labeled with the grade and flow value.
Knowing what can cause discoloration in plastic injection molding can ensure your parts come out sturdy and pristine. If you partner with the right manufacturing company, you can rest assured that they’re aware of the ways to avoid discoloration and other plastic injection defects. We here at Midstate Mold take the utmost care to ensure that our injection molding process is free of mistakes. If you would like to know more about our avoidance of defects or would like a free quote for your project, contact us today.