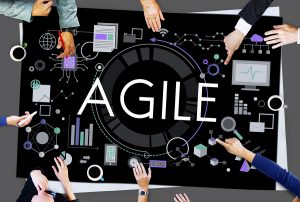
The process from idea to product to market requires many things to go right for a company. There are several factors throughout the entire process, with many of them beyond the control of those involved. When working with your manufacturer, there are specific skills that they will need to possess to help you maximize your efforts, saving you time and money. This is what puts the “agile” in agile injection molding. Learn how it can help you bring your parts and products to market more efficiently.
What Does “Agile” Mean in the Injection Molding Industry?
While it may have become a buzzword in many industries, at its core the term agile is about a company’s ability to adapt. When it comes to the health of your product, from its quality to the speed of production, it’s essential to work with a manufacturer who can adapt, allowing your entire supply and logistics chain to adjust, from changing part designs to switching material suppliers.
Understanding the Term “Lean” with Injection Molding
An accompanying concept to agile manufacturing is lean manufacturing. These are practices and procedures that minimize waste without sacrificing production. This includes concepts such as reducing manufacturing processes that decrease “value” through larger than needed workloads and the conservation of materials. See our blog, Plastic Injection Molding and the Lean Manufacturing Process for more details.
Situations Where Manufacturing Agility Comes in Handy
When you’re exploring possible injection molding companies for your product manufacturing, it’s important to figure out where your potential agile needs intersect with what they can deliver. From helping you quickly come to market to meeting production demands, here are a few ways agile manufacturing can help.
Rapid Part Prototyping
From concept to market, part manufacturing followers four steps: design, prototype, finalization, and production. By bringing in your part manufacturer in during the design phase, they can assist you in designing the best parts with more beneficial attributes and less waste. Learn how CAD files can assist in this process in our blog, Why We Use SolidWorks CAD for Injection Mold Design.
Controlling Costs and Quality
Beyond design, other choices will impact your products cost in terms of both materials and waste from flawed parts. Talk to your tool designer and manufacture about the plastic resins you should use, such as Thermoplastics vs. Thermosets, or which plastic to use. It’s also essential that your manufacturer can meet quality control standards. After all, every flawed part is a cost passed on to you or your consumer.
Meeting Swift Changes in Demand
Lastly, can your manufacturer meet your changes in production with agility? It’s important to discuss your needed volume of production, and how fast they can scale from low volume production to high volume production. The “Push-Pull System,” a manufacturing technique that allows coordination between the manufacturer and you to have the right amount of product ready to go based on expected sales and other variables, meaning as soon as you’re prepared for more parts, they have already been produced.
Here at Midstate Mold, we pride ourselves on comprehensive mold making from assisting in prototype development, tooling design, tool construction and testing, parts production, and parts maintenance. From agile to lean manufacturing, we meet the needs of our customers while keeping committed to quality in all we do. Contact us today to talk to us about your needs in tool and part production for plastic injection molding.