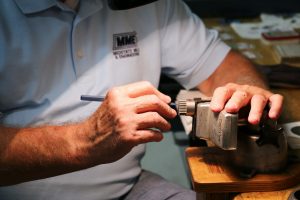
Plastic injection molding all revolves around the use of specially made injection molds – also known as tools or molding tools. Built to exacting specifications, these tools are also built to function under the punishing conditions of high temperatures and repeating cycles, producing hundreds or thousands of parts a day in as many cycles. As these molds wear down, the quality of the parts they make will degrade, causing increased costs and decreased production. Let’s dive into what proper tool maintenance and storage looks like.
Does Your Injection Molding Manufacturer Provide Tool Maintenance?
Does your current or potential injection molding parts manufacturer provide maintenance for their tools? It’s an important factor to consider in order to avoid wear and tear that causes mold neglect. When you’re looking to work with a new molding company, this should be a contributing factor, since repair or replacing a mold is the largest single cost in injection molding. If they do not, do they have a preferred vendor to use? Make sure to learn more about these vendors, their track record, and expected delays during maintenance.
Check out our blog, Avoiding Mold Neglect with Injection Mold Maintenance, to learn more about the issue and why hiring an injection molding company with in-house maintenance might be right for you.
Who Repairs Your Tool When It Degrades or Breaks?
Once a tool goes from wear and tear to breaking, what are your options? Talk to your current molding company about their procedure and make sure to bring it up as part of the hiring and bid process.
- Be Proactive: To begin with, are you making sure your mold is the best mold – not the cheapest one? For example, aluminum molds are easier to make but degrade faster.
- On-site Inspection: Once your mold is finished for the day, is it inspected? Make sure your manufacturer is avoiding the tool breaking due to wear.
- On-site Repairs: Does the manufacturer have a shop for onsite repairs, or will it need to be taken out of the factory? Learn about expected delays during repairs or rebuilds.
Where is Your Tool Stored When It’s Not in Use?
Injection molding tools aren’t in use 24/7, so what happens to your tool when it’s not in use? As we’ve outlined above, inspection and maintenance are a critical part of the process after a tool has seen hard use, but storage is important as well. Is the tool stored on-site if you need to order more parts quickly? Is it kept safe in a climate-controlled area and handled with relative care? Learn more about what happens to your tool when it’s not in use.
If you’re wondering if there are part manufacturers out there who also specialize in mold making, repair, and maintenance, there are: Midstate Mold & Engineering is one of them! We’ve helped countless clients troubleshoot existing molds after relocation, and keep all of their tools in tip-top shape between productions. Contact us today to learn more and get started.